
About the Author:
CEO at AlFiPa, responsible for operations as well as purchasing and sales. He is the primary contact for orders and deliveries within the company.
Composite films for packaging and insulation
Composite films made of plastic, paper, and aluminum are used in a variety of application areas. In the packaging industry, composite films are found in the food sector as well as in industry or pharmacy. Composite films made of plastic, paper, and aluminum are also found in construction and other industries. AlFiPa is your specialist for all types of composite films. With over 40 years of industry experience, we develop composite films that are precisely tailored to your needs.
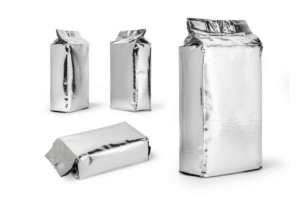
Aluminium composite film is essential for the food industry, as its barrier properties against light, moisture and oxygen extend the shelf life of food. Its efficiency in storage and distribution makes it a key element of modern packaging solutions.
What are laminated films?
Composite films are multi-layered films composed of different materials (e.g., aluminum, plastics, or paper) bonded together. They consist of two or more layers of different materials that are laminated or coated onto each other.
The combination of various material properties allows for the benefits of individual layers to be utilized. The choice of materials depends on the desired properties, such as barrier properties against oxygen or water vapor (moisture), or light. Mechanical properties such as tear resistance, elongation, or thermal resistance also play a role.
What are laminated films made of?
Composite films are made from various materials, each contributing its unique properties to the final product. Here’s a breakdown of the commonly used substances:
- Polyethylene (PE): A thermoplastic polymer known for its flexibility and barrier properties. It can be used in various thicknesses, and with different additives, it can achieve diverse protective or barrier qualities.
- Polypropylene (PP): Another thermoplastic polymer with excellent mechanical properties, often used for its strength and heat resistance.
- Polyester (PET): Distinguished by high transparency, strength, and chemical resistance, PET is frequently used in food and beverage packaging, as well as insulation films for construction due to its good tear resistance.
- Polyamide (PA): Known for its immense tear resistance and toughness, making composite films particularly robust. Generally, PA is even more tear-resistant than PET and is used, for example, with frozen foods.
- Aluminum foil: Aluminum provides an excellent, lasting barrier against oxygen, light, and moisture. It’s used in food packaging to extend shelf life.
- Metalized films: Cover a broad spectrum of applications. While the barrier is not as strong as “real” aluminum, it’s sufficient for most cases. This is particularly true for flexible packaging where products only need to be preserved for a limited time. Therefore, metalized films are used, for example, as packaging films for fast-moving consumer goods in supermarkets. There are also specific uses for metalized films in insulation, especially when a 100% barrier is explicitly not desired.
- Reinforcements such as scrims and fabrics: Scrims and fabrics increase tear resistance and particularly the resistance to further tearing: if such a composite film is torn, the tearing stops at the next thread of the scrim or fabric. Scrims and fabrics can be made of different materials like fiberglass, PET, PP, or PE. They are primarily used in industrial films and insulation. Since the structure of the scrim/fabric presses through to the surface, they are unsuitable for consumer packaging – and moreover, consumers would not be able to tear the packaging with their bare hands.
- Paper: Considered an eco-friendly material, especially when recycled, it can also create a sophisticated tactile feel. Paper is used in composite films for both packaging and insulation. Because paper is relatively inexpensive, it’s often used in insulation to reduce costs.
In addition to these typical materials, the production of composite films can incorporate a wide variety of other film types, including copper, stainless steel, and numerous other plastics. These materials are chosen based on the specific requirements of the application, such as conductivity in the case of copper, or durability and corrosion resistance for stainless steel. The diversity of plastics available allows for a broad spectrum of properties, including UV resistance, flexibility, and bio-compatibility, thereby extending the range of possible applications for composite films even further. This versatility makes composite films a crucial component in many industries, from electronics and aerospace to food packaging and medical devices.
Production process of laminated films
The production of composite films primarily involves two main processes: lamination (also known as laminating) and coating (extrusion). Each method has its own advantages and is selected based on the specific requirements of the film and its intended application.
Aluminum composite film is a key element in the packaging industry, significantly enhancing the longevity and freshness of products. These films consist of a thin layer of aluminum laminated between other materials, such as plastics or paper, to combine the benefits of various materials in a single packaging solution. The aluminum layer provides an excellent barrier against light, oxygen, moisture, and bacteria, making it ideal for packaging food, beverages, pharmaceuticals, and cosmetic products:
- Lamination: In lamination, two or more film sheets are bonded together with an adhesive. Lamination can be performed using various methods:
- Dry Laminating: This process uses an adhesive dissolved in water or solvent. The adhesive is applied to one of the film layers and then partially dried in a drying tunnel. Through pressure and heat, the adhesive is re-melted and the film is bonded to a second layer.
- Wet Laminating: A viscous adhesive is applied to the film. Unlike dry laminating, the adhesive is still wet when bonding the two layers. The second layer is pressed onto the wet adhesive, and the solvent evaporates under pressure and heat.
- Solvent-Free Laminating: Solvent-free adhesives generally consist of two components. When the two components meet, a chemical reaction occurs, creating the adhesive force. Since no solvents need to escape, no drying process is necessary.
- Wax Laminating: In this process, the binder is made of melted wax or hot melt. It is applied to the carrier materials. This method is often used in the lamination of paper+paper or paper+aluminum combinations.
Extrusion:Each of these lamination methods offers distinct advantages, such as the elimination of solvents in solvent-free laminating or the unique properties imparted by wax lamination, allowing for customization of the composite film’s properties to meet specific application needs.
Areas of application for laminated films
Due to their versatile properties and adaptability, laminated films are widely used in many different industries.
Your composite films play a vital role in the packaging industry, especially in the creation of high-quality food and pharmaceutical packaging. The multi-layered structure enables the creation of an optimal barrier against oxygen, moisture, and other external influences. This significantly extends the shelf life of food and pharmaceutical products. Duplex and triplex films that combine materials like aluminum, PE, PET, and others provide an ideal solution for products requiring excellent barrier properties.
In the construction industry, your composite films are used in the building of structures and industrial facilities. Triplex films combining materials such as PET, aluminum, and PE offer absolute barrier properties against oxygen and moisture from water vapor. They also protect against temperature fluctuations and consequently condensation, making them highly suitable for use in insulation materials. This versatility demonstrates the crucial role of composite films in enhancing the durability and efficiency of products and materials across various sectors.
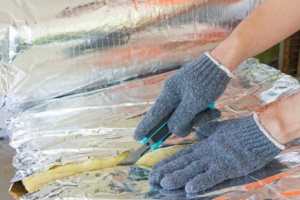
Composite foil is used in the construction industry for thermal and acoustic insulation to increase living comfort and save energy. Its multi-layer structure and easy installation make it ideal for environmentally friendly and energy-efficient construction and renovation projects.
Composite films also find applications in various technical fields, such as in the manufacturing of cables, pipes, turbines, and other technical products. The multi-layered structure allows for the production of films with specific electrical, mechanical, and insulating properties.
Advantages of laminated films
Composite films are characterized by good mechanical strength, meaning they are resistant to stresses, strains, and tears. The use of multiple layers of different materials, including polyethylene (PE), polypropylene (PP), and polyester (PET), allows for the combination of these strong properties with other advantages.
The versatility of composite films is also evident in their ability to withstand extreme temperatures. This temperature resistance is especially important in applications where resistance to cold or heat is required. For instance, in the packaging industry, composite films must protect food from temperature extremes during sea transport.
Barrier layers are a crucial advantage of composite films, significantly contributing to their functionality. These layers, often made of materials such as aluminum, provide a barrier against oxygen, moisture, light, and other external influences, making the films highly desirable for use in food packaging.
The benefits of composite films make them flexible in application. Compared to other packaging materials, such as glass or cardboard, they are also very light. This makes flexible packaging from films both relatively resource-efficient and cost-effective in transport. With just a few kilograms of packaging material, hundreds of kilograms of food can be safely packaged. Composite films and the bags made from them have thus become a key component in the packaging industry.
AlFiPa’s speciality: Customised laminated films
At AlFiPa, customers receive tailored solutions for their needs. That’s because we fully adapt to our customers and their wishes in the production of our composite films. If you want to utilize modern composite films, let us advise you.
Summary
Composite films, made of plastic, paper, and aluminum, are widely used in numerous application areas, particularly in the packaging industry for food, industrial, and pharmaceutical packaging. They are also used in construction and other industries. AlFiPa, with over 40 years of industry experience, is a specialist in custom composite films for use in the packaging industry, construction, and technical fields. The unique properties of composite films, including strength, resistance to cold and heat, as well as barrier layers, make them an indispensable material across various industrial sectors. Their flexibility and the possibility for customer-specific customization underline their significance in modern industry.
For customized solutions and further information, contact us today and get advice from our experts!