
About the Author:
CEO at AlFiPa, responsible for operations as well as purchasing and sales. He is the primary contact for orders and deliveries within the company.
Milk, as a staple food, contains essential nutrients. Therefore, preservation solutions for dairy products must maintain not only the taste, smell, or consistency but also the vitamins and minerals present.
The packaging of dairy products plays a crucial role in this. The challenges faced by dairy product packaging manufacturers vary depending on the type of product, be it whole milk, milk mix products, butter products, or cheese.
Criteria for packaging dairy products
Environmental factors such as light, oxygen, heat, or microbial influences alter the nutrients and vitamins in milk. Thus, dairy product packaging must act as a barrier to ensure the product’s shelf life and its nutrient content. As materials that come into contact with food, they are also subject to strict regulations from official food surveillance authorities.
Food compatibility in dairy product packaging
Hygiene is of utmost importance in the dairy packaging industry. Even slight changes in the contents can lead to reactions posing health risks. Technologies like aseptic packaging concern not only the dairy product itself but also the packaging and the filling conditions.
Furthermore, quality controls in the dairy product packaging industry encompass the materials used. These materials should not contain any harmful substances and must be tailored to the preservation and storage methods of dairy products.
For instance, composite foils used during pasteurization require a special heat-resistant adhesive. Sterilization even places higher demands on the heat resistance of the material.
Films as packaging solutions for dairy products
As food contact materials, plastics demonstrate exceptional properties. They comply with EU guidelines for food compatibility, can be processed in mass production, are moldable, and depending on their composition, can be welded and sealed (FFS films). This allows for materials like Polyethylene (PE), Polypropylene (PP), or Polystyrene (PS) to be combined into composite films. When paired with layers of paper and aluminum, these films meet the complex challenges posed by the packaging requirements for liquid milk, milk mix products, butter, or cheese.
Challenges and solutions for packaging liquid dairy products
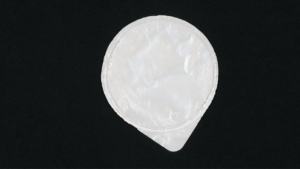
Aluminium lidding films play a crucial role in securing products during transport and storage. Their high barrier not only protects against external influences, but also ensures a hygienic and safe packaging solution for consumers.
Packaging for milk, coffee cream, and cooking cream (whipping cream) needs to be liquid-tight, shock-resistant, and stable. They shouldn’t absorb moisture from the packaged liquid as it would destabilize the packaging. Concerning barrier functionality, the shelf life determines the choice of packaging solution for liquid dairy products:
Fresh milk is perishable and lasts only a few days in a (dark) refrigerator. During this time, water vapor and oxygen cause minimal changes in taste. A three-layer film composite is chosen for packaging. The cardboard provides stability and shields the product from light for its shelf life. A thick PE layer acts as an external liquid barrier, while an inner, thinner PE layer protects the milk from microorganisms in the cardboard and prevents water vapor from softening the cardboard. Alternatively, reusable glass or plastic bottles with a screw cap and a lid film (capsule band) are also used.
UHT (Ultra-High Temperature) milk has a shelf life of several months at room temperature. The composite carton additionally needs an aluminum layer as a long-term oxygen and water vapor barrier and a PE layer to coat the aluminum layer. Bottles with lid films and screw caps are also an option.
Condensed milk can last up to a year. It’s either sterilized using the UHT process and then packaged in a composite carton with an aluminum layer or heated in portion packs made of polystyrene to 120°C (248°F) and subsequently sealed with a film as secondary packaging.
The cardboard provides stability, the PE layers offer a liquid barrier and protection against microorganisms.
Challenges and solutions for packaging milk mix products
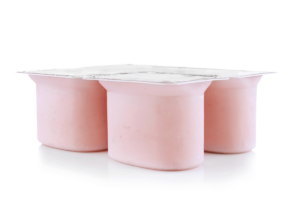
Milk mix packaging benefits from advanced technologies such as FFS sealing film, which ensures optimal sealing and freshness. These state-of-the-art packaging solutions offer an efficient way to safely store and transport dairy mix products while maintaining quality and flavour. An innovative combination for a reliable and high-quality packaging experience.
Packaging for yogurt, yogurt drinks, and milk beverages must be liquid-tight and resistant to lactic acids. They must not harm the contained microorganisms. Their barrier function is limited to the shelf life duration.
For yogurt, sturdy portion cups with foil lids made of metal-coated paper, plastic, or aluminum foil are used. Since the lid receives a lacquered coating on the underside, the dairy products do not come into contact with the processed aluminum.
Yogurt drinks and milk beverages require packaging with a shape and stability that allow for comfortable consumption. Either a three-layer composite carton or plastic bottles with a lid film and screw cap are used.
For quark, depending on its consistency and the filled quantity, portion packs in plastic cups with lid film made of metal-coated paper are suitable, or tube bags made of LDPE housed in light-tight boxes.
Packaging for ice cream must be suitable for deep freezing, meaning they need to be tear-resistant and puncture-resistant. Depending on the contents, there are trays made of plastic or coated cardboard with sealing film and a resealable lid (for portion and family packs) or tube bags made of paper or plastic film (for popsicles).
Challenges and solutions for packaging butter products
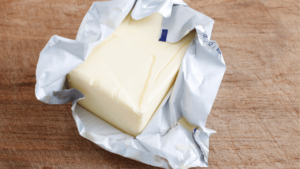
Butter films offer a practical and hygienic packaging solution for fresh butter. Their robust seal keeps the butter protected and fresh, while their easy handling facilitates spreading and portioning
Packaging for butter, clarified butter, and reduced-fat butter must be fat-resistant and fat-tight since butter products can contain up to 90% milk fat.
Depending on the fat content, butter products can quickly absorb odors. Therefore, their packaging serves as an essential barrier against aromas.
Butter wraps, also known as “Butterwickler” or “Buttereinwickler” in German, are duplex composite foils composed of a fat-tight paper layer on the inside and an aluminum layer on the outside to act as a fat barrier.
Clarified butter and reduced-fat butter are sold in solid plastic containers with resealable lids. A sealing film under the lid ensures protection from oxygen, light, and bacteria before the first opening.
Challenges and solutions for packaging cheese
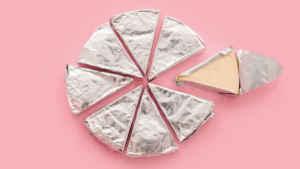
Cheese packaging plays a crucial role in preserving freshness and quality. Modern technologies make it possible to protect the cheese during transport and storage so that it retains its unmistakable flavour and consistency.
Fresh cheese has a high water content, often has a very soft consistency, and requires packaging in an air-tight portion container to prevent mold growth. It is packed in a sealed tube bag under a modified protective atmosphere (vacuum packaging) or in plastic cups with a lid film (gas-flushed packaging).
Soft cheese is sensitive to pressure deformations and often requires solid secondary packaging. The cheese wrapper must be fat-tight. It should prevent direct oxygen intake but remain breathable so the cheese can continue to mature. Thin plastic films or paper foil with an outer PE or aluminum layer meet these properties. To halt or significantly delay the maturation process, gas-flushed packaging in FFS film bags or vacuum-packed shrink films are used for soft cheese. Soft cheeses soaked in whey, brine, or oil (e.g., mozzarella, feta) are sealed liquid-tight in tube bags made of barrier films or laminates with high sealing seam strength (FFS films). Plastic cups with lid films are also used.
Sliced cheese requires packaging that protects against drying out. Suitable options include trays with a lid film or gas-flushed packaging in tube bags.
Hard cheese develops a rind during the maturation process that protects against light, air, moisture loss, or contaminants. Some cheese varieties have a wax layer for this purpose. The packaging primarily protects the aroma and is done in tube bags made of barrier shrink films (vacuum packaging) or in plastic trays with lid films.
Grated cheese is particularly susceptible to mold, which is promoted by air, heat, and light. It requires gas-flushed packaging in a foil bag, such as a stand-up pouch with a resealable zip.
Trends in the dairy packaging industry
The shelf life of dairy products is determined by their production technology. Therefore, product design doesn’t aim to extend shelf life through innovative dairy packaging. Instead, cost-effectiveness plays a significant role in the production of industrial dairy packaging. The protection doesn’t need to extend beyond the specified shelf life, allowing for the potential to save on expensive materials. Moreover, trends in dairy product packaging, such as reducing plastic in favor of cardboard, are moving towards sustainable packaging solutions for dairy products.
Efficient solutions for innovative dairy packaging
Whether it’s efficient industrial milk packaging, eco-friendly packaging solutions for fresh dairy products, or custom-printed dairy product packaging for brands – when it comes to B2B packaging solutions for dairy products, AlFiPa is your competent contact. We advise on materials and technologies for long-lasting packaging for dairy products, also considering sustainable options for dairy product packaging in the B2B sector, and take into account the role of packaging design in marketing dairy products.