
About the Author:
CEO at AlFiPa, responsible for operations as well as purchasing and sales. He is the primary contact for orders and deliveries within the company.
Industrial packaging (Engl. industrial packaging) is often applied during the production process itself. It serves not only to protect goods during storage and transport but also aims for efficient handling of goods during manufacturing. For example, industrial films protect against weather and physical impacts and are also used for stacking and securing goods on pallets. Transport packaging, in addition, enables the transportation of multiple units and simplifies overpacking.
Industrial packaging solutions and their use
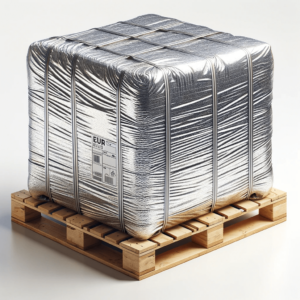
Ideal for heavy industrial goods and machine components, they offer reliable protection against environmental influences and are ideal for the wholesale and export of chemical products and for the electronics industry.
Durable cover hoods made of films and film composites, whose strengths can be customized to customer specifications, offer stable protection against water, dirt, and dust. Thermo covers protect temperature-sensitive products from damage caused by frost, heat, or UV light. They are equipped with a metallized surface and owe their insulating effect to their multi-layered structure with air cushion layers. Aluminum composite hoods provide long-term corrosion protection for electronic products, metal parts, or machinery, and are also used as bulk packaging for export.
Cover, thermo, and aluminum composite hoods are made to customer-specific requirements in various formats. They are used as covers for bulky goods or as protective hoods for crates. Their size can be adjusted to Euro and industrial pallets, allowing them to be easily and quickly slipped over a pallet load. Pallet covers are also used as liners for wire mesh boxes and serve as robust packaging for machine components when loading. In addition to the protective hoods, thermo films are also available as roll goods, which are laid on the pallet and insulate the packed goods from below.
For packaging heavy industrial goods, box hoods or extra-large bags with and without side gussets are used. In accordance with IATA regulations, they are also approved as bulk packaging for the transportation of hazardous goods. Small-format security packaging for industrial products includes flat bags, which are suitable for smaller machine parts and lighter goods. Industrial goods for wholesale are grouped together in bulk packaging (OEM, Original Equipment Manufacturer, first-equipment manufacturer packaging).
Industrial packaging must comply with IATA regulations to be approved for the transport of hazardous materials.
What requirements must industrial packaging and its materials meet?
As protection against weather, contamination, and physical impacts, industrial packaging (industrial packaging) must be not only waterproof but also as resistant as possible to shocks, pressure, or vibrations. Depending on the contents and the application area of the packaging, the materials should also have specific properties:
Optimal Product Protection: Adequate tear resistance and durability are achieved by adjusting the film thickness to the weight and surface texture of the packaged goods.
Welding and Sealing Properties: Protective covers (cover hoods, thermo covers, or aluminum composite hoods) usually have a cubic shape, open at the bottom. The remaining edges are securely sealed. For this purpose, the films used are equipped with a sealable contact layer made of a thermoplastic material, usually PE or PP. Welding the films has the advantage of maintaining the shape and, on the other hand, preventing contamination after packaging.
UV Protection and Resistance: Products sensitive to UV radiation require an opaque, UV-resistant protective cover. UV protection additives in the film absorb UV light and prevent damage to the packaged goods as well as radiation-induced degradation of the packaging material.
Protection Against Tension and Electrostatic Discharge: Antistatic materials prevent the risk of developing tension in packaging for the electronics industry. In addition, special ESD plastics can safely divert electrical charges to a grounded point without causing tension damage to the packaged goods.
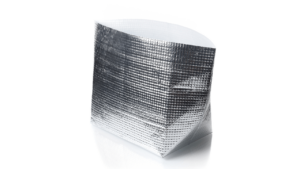
These specially developed bonnets provide excellent thermal protection for temperature-sensitive industrial goods, ensure quality during transport and storage and are ideal for demanding industrial applications.
Temperature Resistance:
Since very high temperatures in summer and low temperatures in winter can occur in closed trucks or transport containers, temperature-sensitive goods are packaged in insulating materials during transport. They slow down the temperature rise or fall and can be a cost-effective alternative to temperature-controlled transport vehicles. For extreme storage or transport conditions, temperature-resistant industrial packaging (industrial packaging) is also necessary.
Chemical Resistance: Depending on the production process and industry, films may be required that are resistant to chemicals (acids, bases, and solvents), oils and fats, and other aggressive liquids.
Cost Efficiency and Universal Applicability: Film packaging for industrial goods must be space-saving, lightweight, and as quick and uncomplicated to use as possible. Ideally, they not only meet the requirements of the mode of transport in goods traffic but are also used as reusable packaging in B2B goods traffic and are also optimized for storage and transport in the plant.
What materials are industrial packaging films made of?
To optimally respond to the requirements, protective covers and films for industrial packaging are composed of various layers. In addition to various plastics and aluminum, textiles are also used for these film composites.
Plastics: Versatility in industrial packaging solutions
Plastic films are easy to handle. As packaging materials, they score with their water-repellent property and resistance to chemical influences, oils, and fats. Films made of PA or PP also have good strength, hardness, and thermal stability. PET films are also resistant to UV light. Depending on the design, PE films show high strength (HD-PE) or good flexibility (LD-PE) and can be used as single-layer cover hoods for industrial goods as well as processed into bubble wrap. Modifying additives are added to the plastics to improve UV protection or an antistatic effect.
Aluminum for improving the film properties of industrial goods packaging
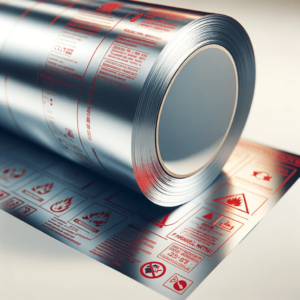
An efficient solution for customised industrial packaging, ideal for high volume and export requirements. This film provides excellent protection for industrial products, including security packaging and applications in the electronics industry.
Aluminum is used for industrial packaging because of its flame-retardant effect and good thermal and electrical conductivity. For example, a PE bubble wrap – provided with an outer aluminum layer – becomes a thermo cover, which not only offers better insulation but also reflects UV radiation. An aluminum layer vapor-deposited on PET film (PET met) can improve its abrasion behavior and increase tear and shock resistance.
Laid scrims, fabrics, and nonwovens in packaging materials for industrial goods
Laid scrims and fabrics are used to increase the tear resistance of packaging materials. To reinforce protective films and hoods, threads are incorporated into the materials to prevent existing tears from extending. These fabric meshes are made of fiberglass or polyester and can be used in conjunction with plastic or aluminum composite films.
Woven films are stretchable, as the incorporated threads are interlaced like textile surfaces. In laid scrims, the threads are in a stretched form. They run parallel and are laid over each other once or several times, crossed. This makes scrims thinner and much stronger than fabrics.
Plastic fibers (e.g., PET, PP) can also be processed into nonwovens. The short, diverse fibers are joined together in a disordered form, are flexible, and are used as antistatic packaging solutions for electronic components.
Packaging trends in the B2B segment
While the optical design plays a role in consumer goods packaging along with durability, industrial packaging solutions prioritize goods protection and logistical optimizations. Strategic packaging design significantly impacts work processes and their efficiency:
- Robust packaging reduces the risk of damage, thereby saving on returns and replacement costs.
- Customized packaging allows for optimal use of storage spaces and truck capacities.
- Easy-to-handle materials save loading capacities and shorten throughput times.
- Standardized packaging solutions facilitate product identification, management, and traceability of their production path.
Furthermore, efficiently used packaging materials not only reduce material effort and packaging costs. They also save CO2 emissions during transport between suppliers and processing plants, contributing to environmental and resource protection. Sustainable packaging solutions for the industry include returnable packaging, circulating between production sites and can be filled repeatedly.
A competent contact for packaging manufacturers
As a specialist in films, AlFiPa is your competent contact when it comes to packaging. Whether your questions concern antistatic materials for the electronics industry, wholesale packaging for chemical products, if you want to develop special customer-specific industrial packaging, or are looking for environmentally friendly packaging options for industrial goods: We have the answer. Contact us!