
About the Author:
CEO at AlFiPa, responsible for operations as well as purchasing and sales. He is the primary contact for orders and deliveries within the company.
Food packaging accounts for nearly 30% of the global packaging market. With a projected annual growth rate of more than 5% until 2028, it is also the fastest-growing segment in the packaging market. In Europe, the consumption of food packaging is also increasing rapidly. According to a forecast by the market research company Ceresana, it will reach 41.7 million tons by 2031.
Flexible packaging, made from various materials such as paper, plastic, or aluminum, is experiencing above-average growth.
These are available either individually or combined in the form of bags, pouches, sacks, or rolls.
They can be used to pack fresh fruits or vegetables, as well as meat and sausage products, ready-to-eat meals, dry foods, snacks, or sweets. Films also serve as sealing lids or are processed into bottle neck tags or coffee capsules.
Films have been used for food packaging since the mid-20th century. Predominantly, pure materials are used that promise economic recyclability. However, in 2022, more than 42% of all film packaging for food in Europe was multi-layered packaging films. These composite materials stand out with their tremendous variability, offering versatile packaging options for various foods.
With an annual growth rate of more than 5% until 2028, food packaging is the fastest-growing segment.
Why do foods need packaging?
Functions of food packaging
Packaging serves various purposes to store food both hygienically and conveniently. Apart from storage, the promotional aspect also plays a significant role in choosing the appropriate food packaging.
- Storage Function: Foods like flour, rice, or peas can only be offered in portions with the help of suitable packaging. In supermarket storerooms, packaged foods can be stacked more space-efficiently.
- Transport Function: Transporting foods without affecting their quality due to pressure, shock, temperature, or moisture is only possible in suitable packaging.
- Advertising and Sales Function: Foods and drinks packed in bottles, cans, or opaque bags require a cover that represents the content of the package. This makes packaging a crucial medium for marketing. Additionally, packaging carries all the necessary product information, such as details about ingredients, nutritional content, origin, or shelf life.
- Protective Function: A primary purpose of food packaging is preservation. It must protect the product from external influences like light, moisture, oxygen, pests, microorganisms, or harmful germs. At the same time, it should prevent germ growth inside the package, halting the ripening process and thus slowing down spoilage.
- Aroma Barrier: Packaging also helps retain flavors by trapping them inside the food packaging.
Health aspects
As objects that come into contact with food (food contact materials), food packaging must meet strict requirements to protect health. This means all packaging must comply with Regulation (EC) No. 2023/2006 and the Framework Regulation (EC) No. 1935/2004, which clearly define which ingredients can be included in packaging.
According to these regulations, packaging materials must not transfer heavy metals, mineral oils, or adhesives to the food, which would impair food safety. The proportion of plasticizers, such as phthalates or Bisphenol A (BPA), which are present in many meat packaging films or in closure caps, must not exceed specified limits. There are also regulations regarding the composition of plastic packaging. The use of recyclates (recycled materials) for food packaging is also limited.
For packaging fatty foods, such as deli meats, large contact surfaces with the packaging film should be avoided. Special regulations also exist for ready-to-eat meals heated in plastic packaging, and for food packaging of acidic or salt-containing foods, like tomato sauce or sauerkraut, which must not come into direct contact with aluminum.
Sustainability
General packaging guidelines at the national level and the EU Packaging Regulation apply to all types of packaging. They aim for sustainable resource and waste management. Consequently, materials that negatively impact the environment should not be used for packaging. Packaging waste should be minimized as much as possible. Recycling should always be prioritized. Therefore, it is essential to ensure that recyclable materials are used in the production of packaging.
Which packaging for which product?
What is currently being done to achieve the goals mentioned above? To optimally meet its functional, health, and legal requirements, the packaging must be precisely tailored to the product.
Factors such as the transportation method or shelf life play a role, as do the consistency and composition of the packed items.
Baked goods
Fresh bread, rolls, and pastries require a sufficiently tear-resistant hygienic packaging that creates an optimal bread environment. This is because only when air can circulate in the bag will the baked goods remain crisp for as long as possible. The classic packaging is a folded paper bag. An embedded window allows a view of the contents. Perforated film provides good air circulation. Films made of PP, PE, or composite films with PET and PA are used for this purpose.
Delicacies
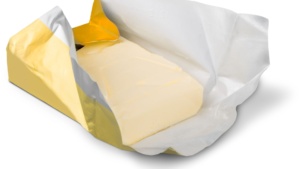
Butter foil
At the deli counter, paper remains the traditional packaging material. Sliced meats or cheeses require a greaseproof and water-resistant version. For filled sandwiches and other snacks, cardboard offers the needed stability. Ready-made salads and pâtés are best protected in sturdy plastic packaging made of grease and acid-resistant materials, like PP or PET. Doypacks or stand-up pouches made of paper-based, plastic-based, or metallized composite films are suitable for candies and roasted nuts.
Fruits and vegetables
Berries can only be offered in appropriate packaging sizes. Fruits and vegetables stay fresh longer when protected from moisture, oxygen, and pests. Many fruits also need protection against pressure damage. Here, sturdy plastic trays or flexible packaging made of PP, PET, or rPET films are ideal. Citrus fruits, onions, or potatoes can be portioned using tubular nets made of PE.
Beverages
Liquids also need to be offered in suitable sales units. Additionally, beverage packaging should be stable when standing, space-saving in storage, and lightweight. Carbonated drinks must also be transported and stored upright. A lightweight and handy alternative to glass is the PET bottle. Aluminum cans also provide good protection from light.
Spices and powders
The primary function of herb and spice packaging is to protect against moisture and loss of aroma. Since aroma protection packages must be sealed at their outer edges, they require materials with good sealing properties. Coffee powder, tea, or cocoa also need protection from heat and should be stored in the dark. Bags and stand-up pouches made from aluminum or paper composite films are ideal for this.
Meat and fish
Packaging for fish or meat products doesn’t only serve as a barrier against external factors. It’s also crucial to inhibit the growth of bacteria naturally present in the product. Additionally, the material must be grease-resistant. Pre-packaged sausages, therefore, appear on shelves in multi-layered film composites (duplex films, triplex films). Raw meat or fish products are wrapped in films that can have up to eleven different plastic layers.
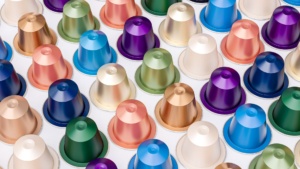
Coffee capsules
Coffee
The packaging of coffee serves not only as a barrier between the food and the outside world to prevent contamination but also has the responsibility of preserving its aroma. Additionally, coffee products are roasted and dried. To maintain this preserved state, the coffee’s packaging should protect against moisture and light. Coffee beans are offered in foil packaging with aroma valves in stores. This type of food packaging ensures stability after filling and protects the product from contamination and loss of aroma. Ground coffee is prone to aroma loss, which is why it should be offered in vacuum-sealed aluminum foil packaging.
Convenience products: Ready meals and frozen foods
Dishes that are cooked in the microwave along with their packaging require covers made of heat-resistant materials, ideally sealed and able to withstand high pressure. Microwave-suitable trays are made of PET, PP, or aluminum. PP is also suitable as a film for cooking bags. Aluminum, due to its high heat resistance, is used to manufacture coffee capsules. Conversely, frozen foods, ice cream, and ready-made frozen meals also require packaging made from temperature-resistant materials.
In addition to cold resistance, packaging bags for frozen food must also have high tear and puncture resistance since the packaged content in its frozen state can often have sharp edges. For frozen products, composite films made of PA and HD-PE are commonly used.
Composite films: Which material has which property?
Films provide the opportunity to tailor packaging material perfectly to the requirements of the contents. Different layers can be combined into a composite film, making the best use of their respective advantages. Mostly plastics, aluminum, or paper serve as base materials. The processed film layers bestow their characteristics upon the composite:
Paper is an affordable and lightweight packaging material. It’s biobased, recyclable, and prints well.
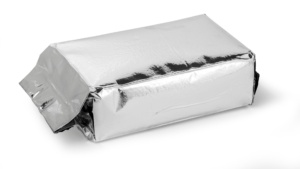
Aluminium foil
Aluminum weighs only slightly more than plastic or paper. It’s opaque, acting as a barrier to both oxygen and moisture, thus protecting the product from losing its aroma.
Plastic is lightweight yet simultaneously flexible and sturdy, offering excellent protection. It is the most commonly used packaging material in the food sector:
- PET – Polyethylene Terephthalate stands out for its resistance to fats or alcohol and is also used for vinegars or oils. It’s the only plastic that can be recycled without loss of quality (rPET – recycled Polyethylene Terephthalate).
- PP – Polypropylene is free from plasticizers and is characterized by its resistance to fats and many acids and alkalis, as well as by its high heat resistance.
- PE – Polyethylene has good welding and sealing properties, contains no plasticizers, and is suitable for direct contact with meat or sausage. It’s available in versions with different densities, which vary in transparency, flexibility, and temperature resistance. HD-PE (High-Density Polyethylene) is found in sturdy film bags. LD-PE (Low-Density Polyethylene) is also used for the inner lining of beverage cartons.
- PA – Polyamide is resistant to extremely low temperatures and has high puncture resistance.
Coated films can also be varnished or printed, opening up vibrant possibilities for packaging design. Additionally, special solutions for preserving food can be applied to film packaging. By modifying the gaseous space between the packaged goods and the film, shelf life can be significantly extended (vacuum packaging, protective gas packaging). Integrated filters, oxygen absorbers, or coatings in the packaging can reduce moisture and halt the growth of germs (Active Packaging).
Current trends in packaging films for food
Over the past four years, the use of paper-based composite films for food packaging has increased by 50%. This reflects the current strategies in the packaging industry:
- Modification of the raw materials for packaging
- Enhancement of the properties of films
- Improvement in recyclability
- Replacement of fossil resources with renewable materials
Paper films are biodegradable, compostable, and recyclable even when combined with cardboard packaging. They can be made entirely transparent and, after specific treatment, can perform barrier functions similar to plastics.
Increasingly, bioplastics and bio-films are emerging as alternatives to traditional plastics. They are made wholly or partly from renewable resources such as corn, sugarcane, or potatoes. Ethylene derived from sugarcane possesses the same properties as its petroleum-based counterpart. Bioplastics made from Polylactic acid (PLA) can be used similarly to PET.
Simultaneously, there’s a shift from multi-material films to mono-films. Packages made from these uniformly produced films are easier to separate, making the recycling of such film packaging profitable.
And what does the future hold?
The packaging of tomorrow is edible. It’s made from proteins derived from plants, fungi, and algae and is coated with a protective layer of fats, waxes, and polysaccharides. And it’s smart. It monitors the condition of its content, communicates with an intelligent refrigerator, and connects to a smartphone.
Although there are calls for a more environmentally friendly lifestyle that includes removing packaging entirely, it’s worth noting that unpackaged foods are unprotected foods. They spoil faster and, in the worst-case scenario, get discarded.
Packaging thus also plays a role in preventing food wastage.
With our development of food packaging films at AlFiPa, we bridge the gap between the stringent requirements of food quality assurance and sustainable resource use. Do you need expert advice on optimizing your packaging? Contact us!